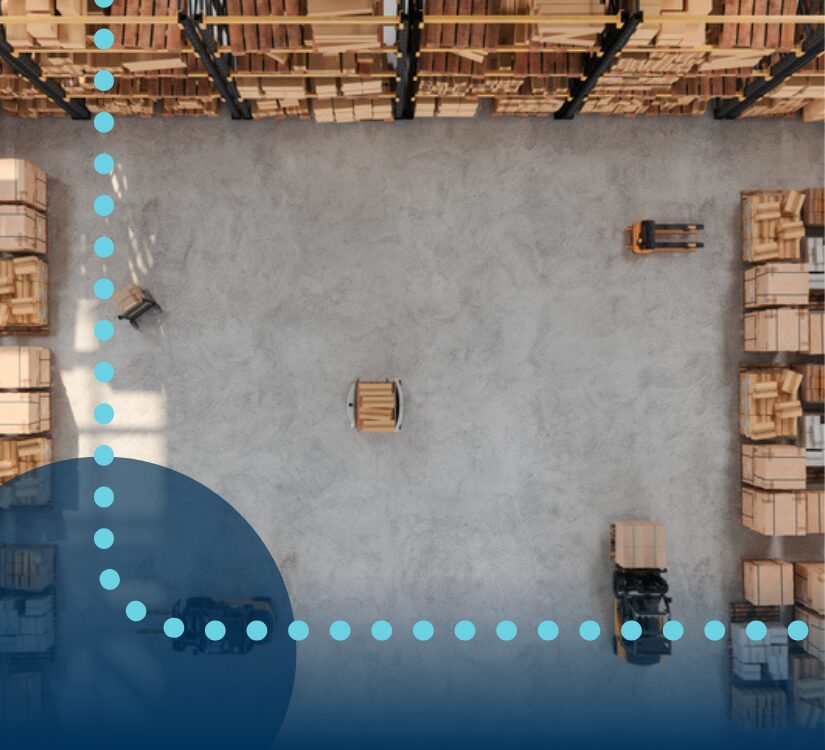
Warehouses dedicated to fulfillment operations are becoming increasingly scarce and rental rates are skyrocketing as demand rises. The Journal of Commerce reported that the national vacancy rate of industrial space is about 5 percent and industrial rents have increased 8 percent this year.
The demand for more warehouse space is felt across the country. In New Jersey, the largest area of space currently available is 500,000 square feet. The amount of industrial warehouse space added in the state this year is on track to exceed last year’s 4 million square feet as developers are rushing to keep up with demand.
Retailers are trying to move into the most optimal warehouse spaces, and there’s “little to no vacant existing product available,” reported real estate firm Jones Lang LaSalle. With fulfillment operations accounting for nearly 40 percent of all warehouse space in America, what are companies that are struggling to expand their reach supposed to do when space is difficult to find?
Analysts from the reports cited above suggest that you should optimize the warehouse space you already own rather than look for more. Restructuring your operation to drive efficiency in a facility that already belongs to you is a budget-friendly alternative during an era of high demand and real estate shortage. Let’s explore several ways you can optimize your already established facility.
1. Upgrade Inventory Visibility
Accurately viewing real-time inventory levels and tracking demand patterns is critical to your ability to identify obstacles before they affect the rest of your operation or customer relationships.
Retailers look for additional warehouses so they can place inventory closer to consumers, but a better inventory management system can provide similar results if you don’t have the means to purchase additional space.
Instead of opening a new warehouse, use the data you’ve collected regarding inventory levels and customer demand to transfer products throughout your already established network of warehouses. If demand for a specific region is analyzed and inventory levels are too low to meet it, then you have the power to move and better position the product near where it’s wanted without opening a new facility.
2. Improve Warehouse Layout
Along with increasing inventory visibility, changing the layout of your warehouse can also boost efficiency.
Utilizing vertical space is a great way to maximize the facility you already own, especially as inventory volume rises. Operational leaders can take advantage of the vertical space above docks, cross aisles, work areas or any other empty space, as long as it doesn’t present a safety risk.
The 80/20 principle can be applied to most areas of business, including warehouse operations. Approximately 80 percent of your sales are coming from 20 percent of your products. After determining what products are ordered the most, modify your warehouse layout so those items are the closest to the packaging area. It’ll save time by reducing workers steps in the warehouse, thus increasing fulfillment speed.
Taking this idea a step further, you should also use customer shopping data to determine what items are frequently ordered together. Items that are commonly shipped together should be placed near each other for the same reason that popular items should be located close to packaging areas.
3. Ramp Up Staffing & Streamline Workforce Processes
Rather than spending a large chunk of your budget on a new warehouse as a way to reduce shipping time, use that money to hire additional workers. The more workers you have the more orders you can fulfill.
One helpful step to drive picking and packing efficiency is to reduce the number of times a package is touched. In other words, one worker can pick and package an item and have it ready for delivery rather than transfer the item from station to station for it to be checked and packaged by someone else. Each additional touch slows down the fulfillment process by decreasing product flow.
A second option is to minimize movement. As mentioned above, walking around a large warehouse can slow down the fulfillment process and make the worker more tired or prone to making mistakes. The additional workers available can allow you to easily implement a zone-based picking strategy: a method that divides inventory into different zones in the warehouse. Each worker is trained to pick in their assigned zone, which reduces steps taken and can maximize efficiency.
Proper management of this workforce is another area to invest in. Partnering with a staffing provider that works onsite and manages day-to-day workforce performance is essential for increased productivity.
4. Consider Warehouses Outside of Prime Markets
If more than 85 percent of your warehouse space is being utilized, and you’ve implemented the above strategies, then it may be time to move into a new warehouse. But is competing for overpriced real estate in prime markets the only option?
Thankfully not. In fact, secondary industrial markets have great potential. A study released by commercial real estate firm CBRE revealed that the need for a greater supply chain presence outside major areas is accelerating the warehouse growth in secondary markets.
These smaller markets, such as Denver, Las Vegas and Portland, Oregon, are attractive because of their more affordable rents. The average rent in the 17 U.S. secondary markets defined by CBRE rose 13 percent since 2011, which is less than half of the rate increase for primary markets. Additionally, several of these secondary markets are popular with Millennials, indicating that they could be prime targets for ecommerce growth.
Although order volume may not currently be as high in the secondary markets, the demand is diversifying as consumers from any part of the country are able to order online. Ecommerce is not exclusive to large metropolitan areas, so opening operations in smaller, strategically chosen markets can save you money while still giving you the ability to meet customer expectations.
Optimizing Your Established Facility
As you begin noticing that you may need additional warehouse space, your first reaction may be to open a new warehouse. But real estate shortage and high rental rates can make this challenging. Instead, strengthen processes and areas in your already established warehouses, such as inventory and workforce management, to get the most out of the space you already own.