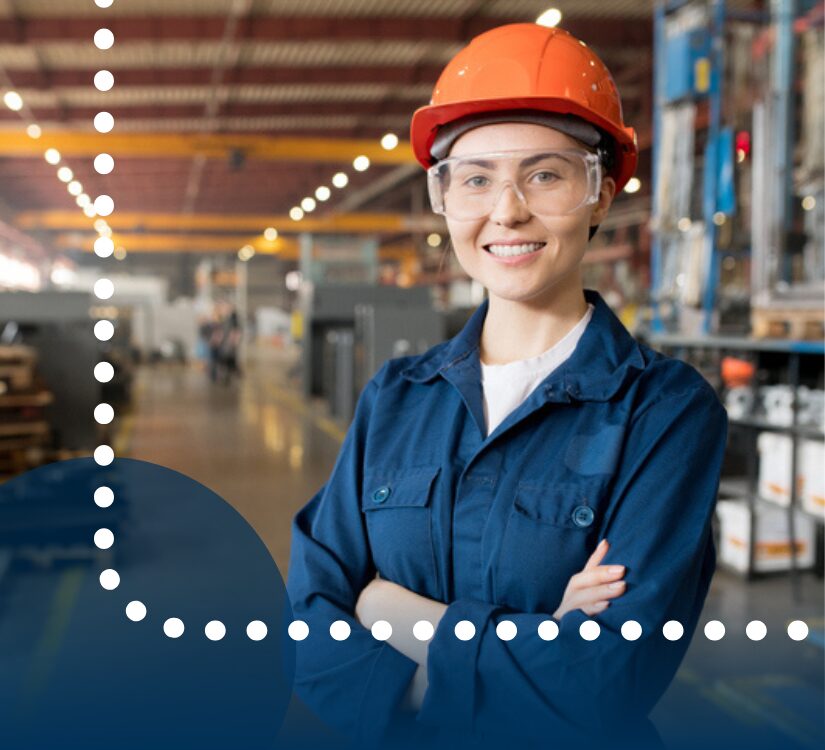
We’ve all heard about the manufacturing skills gap that’s making it challenging for companies to find skilled employees; there simply aren’t enough workers available who possess the needed skills.
The manufacturing industry has rapidly become more complex with the addition of robotics and other technological advancements, like IoT, further widening the skills gap. Unfortunately, the additional interest gap that blankets the industry is only making it more challenging.
But manufacturers may feel relief soon. According to a recent study conducted in part by Massachusetts Institute of Technology’s Sloan School of Management, less than a quarter of manufacturing plants had production worker vacancies that lasted for three or more months.
Additionally, a Boston Consulting Group study revealed that only five of the 50 largest U.S. manufacturing hubs – Baton Rouge, Louisiana, Charlotte, North Carolina, Miami, San Antonio and Wichita, Kansas – are suffering from a serious skills shortage.
While there’s evidence that the manufacturing skills gap may be shrinking, it’s still causing headaches for many companies that operate in remote areas or tough labor markets. If you’re one of these companies that’s still feeling the negative effects of the skills gap, here are three things you can do to attract and retain skilled workers.
Foster Community Partnerships
Manufacturers can partner with local universities, community colleges and vocational schools to generate interest in the industry and provide students with a technical foundation before they enter the workforce.
A Kentucky Toyota factory partnered with a technical community college in the area to create the Advanced Manufacturing Technician Program where students can enroll in hands-on classes directly inside of the Toyota plant. Upon completion of the program, students receive an associate’s degree and many are even offered full-time employment.
These types of programs not only generate interest in your company but also fill your candidate pipeline with skilled workers. Toyota can be confident they’re receiving quality talent to advance their operation since they’re able to influence the students’ curriculum.
Some manufactures are targeting future candidates even before college. The Golden Corridor Advanced Manufacturing Partnership, which represents about 20 manufacturers in the Chicagoland area, partners with local high schools to create a premature talent pipeline. The group offers student internships, sponsors robotics contests, donates equipment and hosts open houses to give students an inside look at their facility.
Contingent Workforce Tip: Your staffing provider should already have partnerships built with local organizations as part of their recruitment strategy. You can use these already established relationships as starting points to initiate programs similar to the ones discussed above.
Improve Onboarding
When was the last time your company reviewed its onboarding process? Revamping this process to be more informative and engaging can accelerate the productivity of new employees.
A thorough and well-executed onboarding process gives new hires the impression that your company values its employees. It also allows employees to better connect company-wide goals to their daily tasks making them feel a part of a bigger picture. Effective onboarding has even been shown to boost new hire productivity by 70 percent.
Not only is a strong onboarding process good for engagement and productivity, but also for reducing turnover. HR news site TLNT found that 73 percent of organizations update their onboarding process to improve employee retention. This is an important area of investment for manufacturers as turnover continues to be a costly line item. Replacing a line worker, for example, can cost about $5,000.
So, what are the essentials of a great onboarding process? Here’s three:
- It should be personalized and welcoming
New hires can be partnered with a tenured and friendly employee to shadow during their first week so they can adjust to the facility layout and new processes and meet coworkers right away.
- It should convey company culture, values and mission
This allows the new hire to understand your company better, build skills aligned with business goals and determine how they can be an asset to the team.
- It should address compliance and safety
Discussing these topics can prevent future safety risks and issues in your facility and lets the employee know exactly how to handle unsafe situations when they do arise.
Contingent Workforce Tip: It’s important that your staffing partner’s onboarding processes are aligned with yours so that all workers within your facility have the same information. An onsite provider that can manage the onboarding requirements for your contingent workforce is a plus because they remove this responsibility from your team.
Implement Learning Opportunities
Training shouldn’t stop after the initial onboarding. Instead, manufacturers should establish continuous learning and advancement opportunities for their current workforce. On-the-job skills are quickly becoming outdated as manufacturing facilities’ technology evolves. Investing in ongoing training for your workforce prevents you from having to search for new talent with advanced skills when technology improvements are made.
By not providing skill-building programs, you can put your facility at a disadvantage by discouraging top talent to stay. Nearly 53 percent of employees are likely or very likely to leave their position because of ineffective opportunities for growth and learning.
Jeff Weber, senior vice president at educational technology company Instructure, details four components to include in a manufacturing training program:
- Mobile-Enabled
If your team is unable to reach your workforce in-person because of differing shift times or locations, going mobile is a good solution.
- Easily Consumable
Training takeaways should be easy to remember and easily accessible when needed for a particular task. Make sure the information provided is concise, helpful and engaging.
- Safety-Focused
Safety should always be at the center of your training to ensure workers are aware of your facility’s safety guidelines and know what preventative actions they can take to reduce risks.
- Unique
Employers should offer skills training that workers can’t find anywhere else. This information can come from the experiences of managers and executives.
Contingent Workforce Tip: Your contingent workforce provides a great pool of candidates to draw from when you are looking to hire additional employees. Look for a staffing partner that is actively involved in the performance coaching and management of these workers.
Is the Manufacturing Skills Gap Shrinking?
The effects of the manufacturing skills gap are still very real for many employers. The good news is that there are many ways you can work to minimize this gap and improve your talent pipeline.
Companies can begin by partnering with local organizations to target future candidates and drive interest in manufacturing. They can also revisit and revamp their onboarding processes to ensure new workers understand company goals and expectations. Finally, as skills become outdated, making learning and growth opportunities available to current employees will deter them from seeking employment elsewhere.
Looking for more strategies to attract manufacturing talent? Check out our white paper, Key Strategies for Success in the Light Industrial Recruitment Market >