Recruiting Tips: Hiring for the Future [Guide]
Get the Guide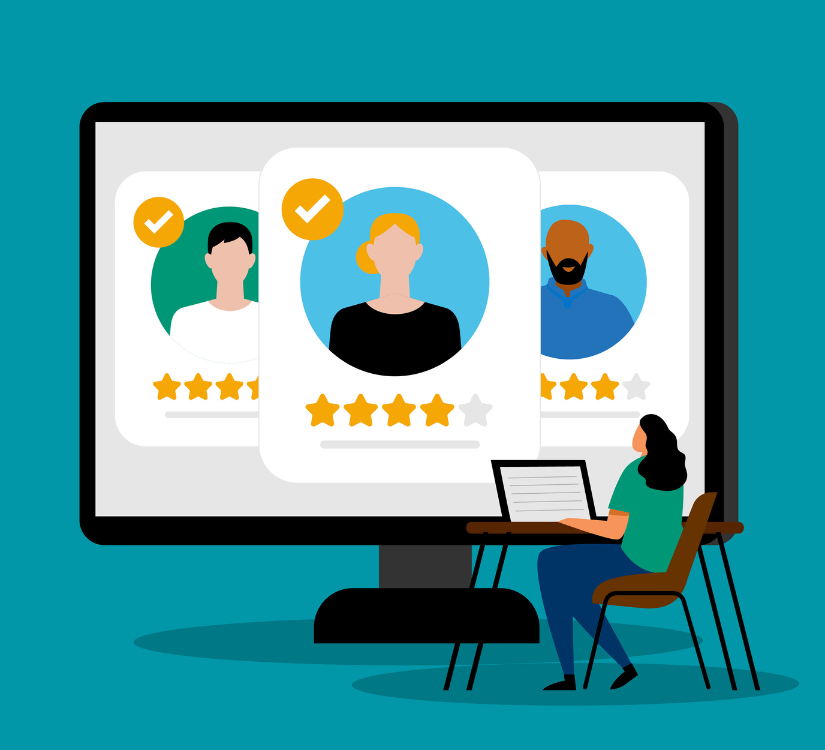
Struggling to get employees excited about safety? Watch our video for four creative ideas to transform your safety program and boost engagement.
As leaders in the staffing industry, we’ve truly seen it all and we want to share that knowledge with you. Here are the top 4 emerging trends for recruitment in 2025.
Cementing its status as a leader in recruiting and staffing, Staff Management | SMX ranked No. 94 on Forbes’ America’s Best Temp Staffing Firms 2025 list.
This quick guide will outline the benefits of a comprehensive program, how to motivate your employees and some creative safety program ideas to get you started as well as a safety checklist.
In the past few years, there have been drastic changes to the recruitment and hiring process. This guide offers practical strategies to streamline your recruiting process, from initial job posting to using data to inform your next move.
The key to a culture of safety is to encourage safety in the workplace for all employees. We have 5 strategies to implement in your organization.
At Staff Management | SMX, safety is a part of our daily operations and we work with each client to ensure their safety program is tailored to their operation.
The U.S. labor market kicked off 2025 with some solid momentum, but things are changing quickly under the surface. Here is a quick Q1 2025 recap and how you can turn these takeaways into forward momentum.
Both temp-to-hire and direct hire staffing solutions offer many benefits to your organization. Read on to discover which one will reign supreme!
Document fraud has become an increasingly sophisticated challenge for employers. This quick guide provides tips to identify red flags, implement verification protocols, and protect your organization from potential compliance document fraud
Across the country, businesses are evaluating many aspects of their business including areas they could consolidate and improve efficiencies within their overall business supply chain
Preparing for a compliance audit can feel overwhelming. Take the guesswork out of compliance and use our checklist to prepare proactively for your next review.
TrueBlue is pleased to announce a strategic partnership with OMNIA Partners, a leading group purchasing organization (GPO) to help businesses across the private sector source more efficient workforce solutions.
The Americans with Disabilities Act (ADA) was created to ensure that people with disabilities can participate in life equally. Here’s how to create a disability-friendly workplace.
Child labor remains a critical global issue that threatens the well-being, education and future of millions of children worldwide. Here, we dive into the importance of preventing child labor, the severe consequences for employers, and practical strategies to identify and combat this harmful practice.